Rapid Improvement Event (RIE)
For the half dozen or so hospitals that hit this page every day, it’s apparent your focused on how to accelerate results with this important tool – the Rapid Improvement Event (RIE). Why not contact us?
Lean organizations are learning organizations. This glossary definition is good, but a conversation would be better. You can get me at jtimpson@kaufmanglobal.com. I’ll be happy to answer any questions and I’m sure I’ll learn something too. Perhaps I can recommend some additional materials that might help. ~ Jerry Timpson
===
The Rapid Improvement Event (RIE) is a standard approach to team-based problem solving. The RIE helps teams focus on process problems that are beyond the day-to-day work. The Rapid Improvement Event is a fundamental and popular Operational Excellence technique.
Rapid Improvement Event Approach
RIEs are highly facilitated sessions that bring a team together, usually 5 to 9 individuals who work within the process along with representatives from upstream (suppliers) and downstream (customers). The standard sequence of events is:
- Define the scope and form the team
- Kick off the event and train the team in the basics (Lean, waste, problem solving, teamwork, etc.)
- Map the process and collect data
- Dissect the problem into its elements
- Develop and prioritize solutions
- Report results
- Close action items according to plan
The work utilizes an array of Lean and OpEx tools and techniques. The RIE is chartered, with a tightly defined scope and usually lasts between 3 and 5 days and includes real-time training, an executive champion and a final report-out to interested and affected parties.
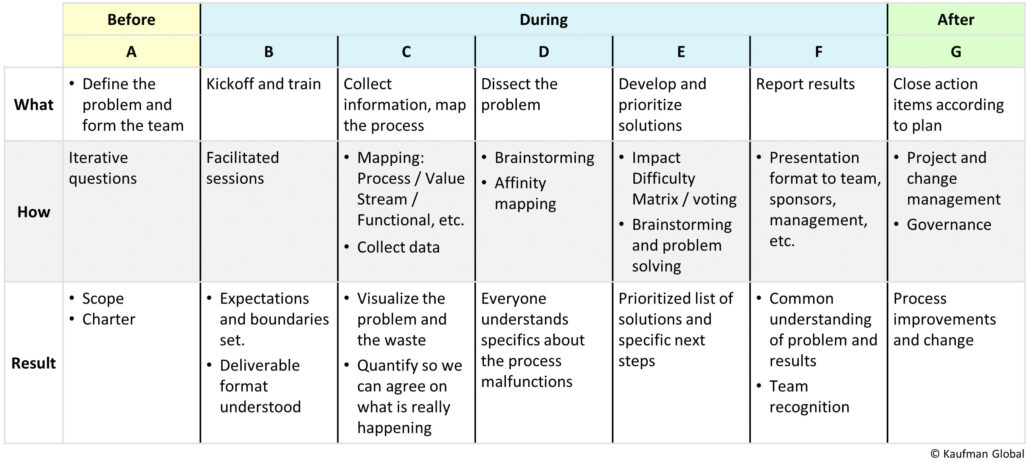
Basic steps for any Rapid Improvement Event
Rapid Improvement Event Scope
The RIE can be applied to any process problem – manufacturing, business process or service. It is important to limit the scope to something that a small team can tackle in a week or less of highly focused process improvement work. Lean and process improvement techniques such as Value Stream and Process Mapping, and Hand-Off Charts and RACI Diagrams are often applied during the Rapid Improvement Event.
Kaufman Global Provides Full Service RPE Facilitation and Coaching
Why not hit contact and ask us about how we do this?
Notes:
Want more detail? A three-week guide to Kaizen Event planning, conduct and follow-up can be found here in our Kaizen 101 blog post.
Find out more about how to really make the Rapid Improvement Event work in this exciting blog post: Rapid Improvement Event Fundamentals
To learn about Kaufman Global’s related services, go here: Kaizen Events
Other names for the Rapid Improvement Event: Kaizen Event, Accelerated Change Process (ACP), Work Out, Change Acceleration Process (CAP), Process Improvement Process (PIP) and the list goes on.
With all the attributes of a Kaizen Event, the term “Rapid Improvement Event” was originated by Kaufman Global in the 1990s for two reasons:
- To expand the application of focused problem solving events beyond manufacturing and into business process and service environments. At that time, Kaizen Events were predominantly seen as techniques for improving manufacturing and production work cells.
- To establish a naming convention that more accurately describes the expected outcomes.