Posts
An Afternoon Spent Process Mapping is an Afternoon Well Spent
/in Grab Bag /by Kaufman GlobalEarlier this month we spent a few hours with the great team at Jefferson Electric to help them do their first process mapping exercise. They are thinking hard about how to be more effective and standard in the ways they work so that they can continue to grow their business and provide opportunities for new team members to join their organization. We had a great time learning about their solar business and seeing them collaborate as a cross-functional team — really getting to the nitty gritty of how they can better connect their sales and field operations. No team is too small to tackle making positive change — it benefits the internal and external clients and enables agility and responsiveness! #solar #jeffersonelectric #teambuilding #CIisforeveryone
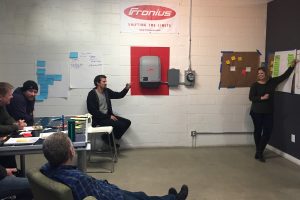
Team discusses identified improvement opportunities and ranks them via use of an Impact Difficulty Matrix
4 Tips To Simplify Work Complexity
/in Tools and Methods /by Jerry TimpsonComplexity means more options for failure.
People and processes come together to deliver products and services. Like a ball of string collected, complexity builds as things are added to accommodate the dynamic environment: organizations, procedures, technologies, reporting, etc. This “growth” happens incrementally and naturally in every business. Simplification can overcome complexity, but it takes energy to accomplish.
When two entities merge and attempt to integrate, the chaos is more obvious. Either way, the interactions are seldom or appropriately examined to determine what can be eliminated. Ultimately, the patchwork of fixes and micro-solutions generate systems that are more complex than they need to be. They are difficult to understand, standardize and control.
Complexity doesn’t automatically resolve itself. Some organizations endeavor re-design from time to time, but the work is typically limited in scope and stays inside functional boundaries. Here, there are plenty of examples of success in areas like Finance, Manufacturing, Product Development, etc. When we explore enterprise value streams that cross boundaries―for example the alignment of Sales, Product Development and Production, it gets a little tougher. Even so, opportunities to improve competitiveness are vast, therefore it makes sense to take a broader approach and navigate the stream through the enterprise. Results are more assured when the initial work is well planned and executed with precision.
1. Inclusive Workshop Aimed at Reduction
A structured workshop is the best way to begin. This may be a single event or a series of sessions. It goes beyond getting a few people together to compare ideas. Top considerations are:
- Leadership engagement (governance)
- Simplification Team participants and
- Implementation imperatives.
To determine scope, start with the system of people and processes that you have; the current state. Some will argue it’s better to begin with a clean-slate, but really, there is no such thing. In rare situations where there is no process to begin with, gaining a systems understanding without preconceived notions is more or less impossible. Besides, in most cases, products or services are already flowing. So start here to decipher the variables that are adding value.
2. Governance and the Politics of Change
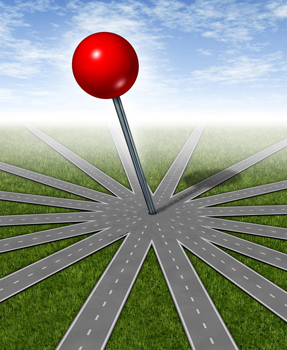
Once you’ve got an idea about the scope of work, it’s time to get the right leadership engaged. First, determine the major processes and or functions that are part of the system. Then identify the single point of control for all of them. For many organizations, the control point for value streams that bisect the enterprise is the CEO. This isn’t so surprising when you consider the rich mix of silos, shared services and dual reporting structures that exist within most organizations. Single-point control at high levels is the main reason simplifying enterprise value streams is difficult, and why we often settle for optimizing functions or sub-processes. Don’t settle.
The control point then directs the functional leaders to participate by forming a coalition to govern the progress of the workshop (and beyond). This direction is the catalyst for action and it is a critical step. The task often requires more effort than initially expected, so be prepared with enough up-front work to make an effective case for change.
3. The Simplification Team – Dealing with Data, Facts, People and Emotion
The workshops are staffed by individuals who work inside the existing system and therefore understand the most about what it delivers and how it functions. They also tend to defend the status quo but will probably be part of the change moving forward, so get them involved them early. You’re digging into things that people have built over time. Don’t underestimate the work required to keep this team motivated and on track.
Include some who don’t operate the existing system to get an unbiased view and to ask the “obvious” questions. In the ensuing conversations, you’ll hear “You don’t understand.” a lot – which is exactly what we want. Through these interactions, the team gains clarity about the system as a whole, instead of just their part of it.
4. Consider What Comes Next
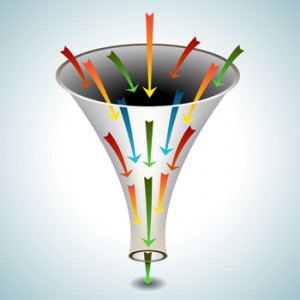
The workshop decision is taken, simplification is an objective, the processes and people are known and an accountable Steering Team is enlisted… all good. So far the task at hand doesn’t seem too daunting. Now, as part of the workshop, go beyond simplification design and consider implementation. What will it take to operationalize the changes?
Workshops get things rolling by providing an output that describes processes at a high level. As the future state becomes current state in the real world, change is managed and kinks are worked out in-situ. The new system is built by standardizing processes as they emerge and then attaching and adhering to relevant procedures. Don’t add complexity back in by over-prescribing. Simpler definitions are more likely to be adapted, provide fewer options for things to go wrong and give more room for value-driven decisions to be made at the right level.
***********************
Complexity happens naturally. Simplification does not. People are frustrated working in bloated, ineffective and inefficient systems. There are no silver bullets, but smart design is a great starting point. Use an inclusive, holistic approach to extract solutions, identify value and restructure the work. Then engage the organization for extraordinary results.
Stand Down Events for Truly Rapid Results
/in Tools and Methods /by Kaufman GlobalOver the years, businesses have used numerous tools and techniques to achieve rapid change (i.e., Kaizen events). These techniques have typically focused on resolving specific manufacturing or business issues and last (often) for five days. However, in today’s fast-paced world, shutting down for an entire week to find and implement solutions to known problems is most often considered out of the question. Businesses now expect immediate gratification, often aiming at big changes in a just one day.
With a “need for speed,” more and more organizations are adopting the idea of holding what are best known as Stand Down Days ― one-day problem solving events. These intense initiatives can be focused on a broad range of improvement activities, but are most often leveraged to jump start 5S programs. Far removed from “business as usual,” a Stand Down Day is not something that can be undertaken by the faint-hearted. Only organizations with true diligence will succeed.
For Lean aficionados, the execution of a Stand Down Day should not be that daunting, as it falls squarely within the typical framework of Plan-Do-Check-Act (PDCA) ― with a significant emphasis on the P. The primary objective of any Stand Down is to orchestrate a series of tasks in a day that could typically extend over weeks of uncoordinated activities. Such orchestration needs more than a maestro; it requires music sheets and the combined skills of an entire orchestra.
There can be no half-measures in accepting such an undertaking, and it all starts with 100% buy-in from the Site Leadership Team. This means wholehearted involvement from top management to commit their entire workforce. In fact, first and foremost, Leadership must agree to shutdown all normal operations and office activities for the day in order to have a single site-wide focus of creating a “world-class” working environment. There can be no exclusions! Leadership must also ensure that all employees understand the significance of what is being planned, and that their participation in the outcome can have a far-reaching impact on the overall success of the business.
The implementation of a 5S Stand Down Day needs to be looked at as an opportunity for the entire business to work together as a well-oiled machine. If one cog in the wheel is failing, the entire machine malfunctions. Due to the time restraints, nobody can afford to nibble around the edge of a problem that has suddenly become everyone’s problem. Instead, it must to be tackled as the only gorilla in the room. There is perhaps no greater motivation than this kind of peer pressure to deliver immediate and tangible results.
To learn more about how to most effectively plan and execute a Stand Down event, click here to download Kaufman Global’s white paper, “Stand Down Events for 5S: The Thirst for Rapid Improvement.”