Project Highlights
Deploy a standard approach to Lean across a global footprint
Train 13 Lean Leaders representing 10 sites and 4 countries
Integrate with existing 6σ program and SAP
Targets: cycle time, cost, yield, capacity, customer service
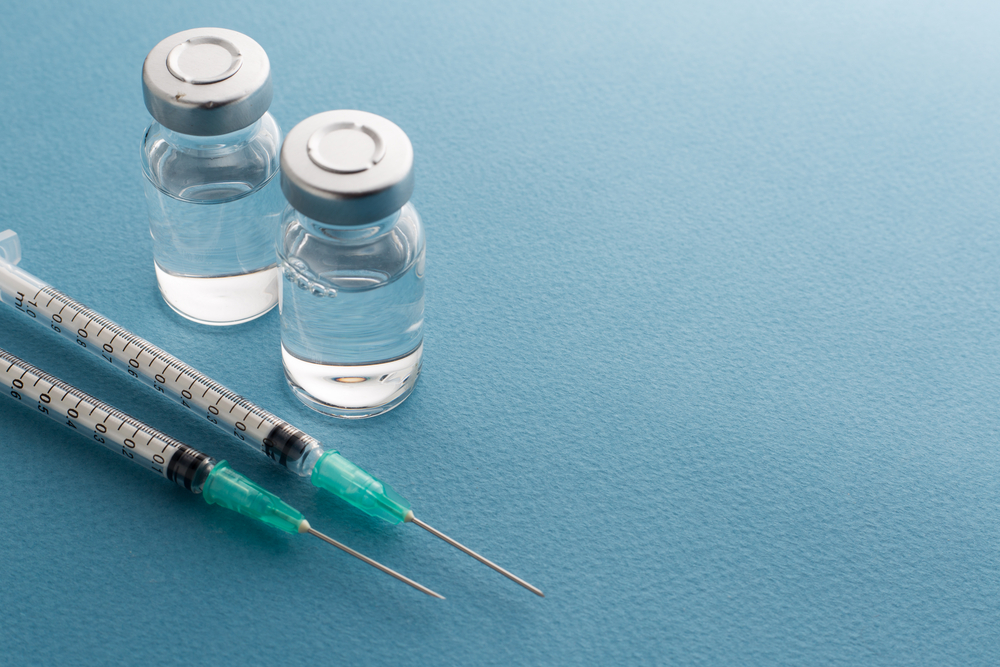
Realized savings Yr 1
Employees engaged
Finished units saved
Lean Leaders deployed
Inventory reduction
Deliver a total solution, from training to on-site Lean support.
A producer of specialized medical products and services had relied for years on technology, product innovation and marketing as its main competitive weapons. To further differentiate itself, the client needed to elevate its internal capability by establishing a standard approach to operations and continuous improvement. Radical changes would be needed to generate significant, tangible results.
Kaufman Global conducted our Lean Leadership® flight training program, enabling high potential leaders to champion the organization’s Lean strategic intent and associated business goals. Phase one lasted 12 weeks and included several weeks of classroom training interspersed with nine weeks of on-site, practical application. Local plans were developed for each site and Lean Leaders were coached on change management. Site leadership teams were enrolled in Executive Steering Committees and employee engagement was driven at the workgroup level via LDMS.
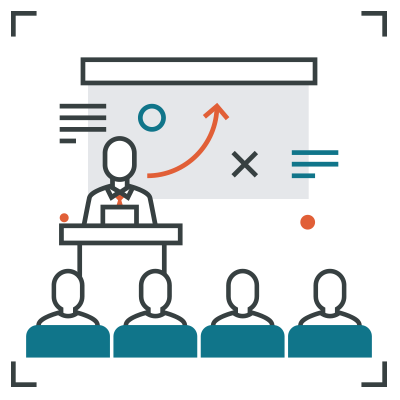
“We will significantly improve our competitive position if our operational ability is elevated to align with our marketing, technology and new product introduction.”
Vice President, Worldwide Business
Get Results
Like These.
Real organization change requires fast action, fast impact and enduring confidence in their results. Put Kaufman Global to work for you.