Project Highlights
Multi-site projects – commercial / light vehicle
Productivity, throughput, quality, revenue
Prepared internal consultants to sustain performance
Harmonized with corporate CI program
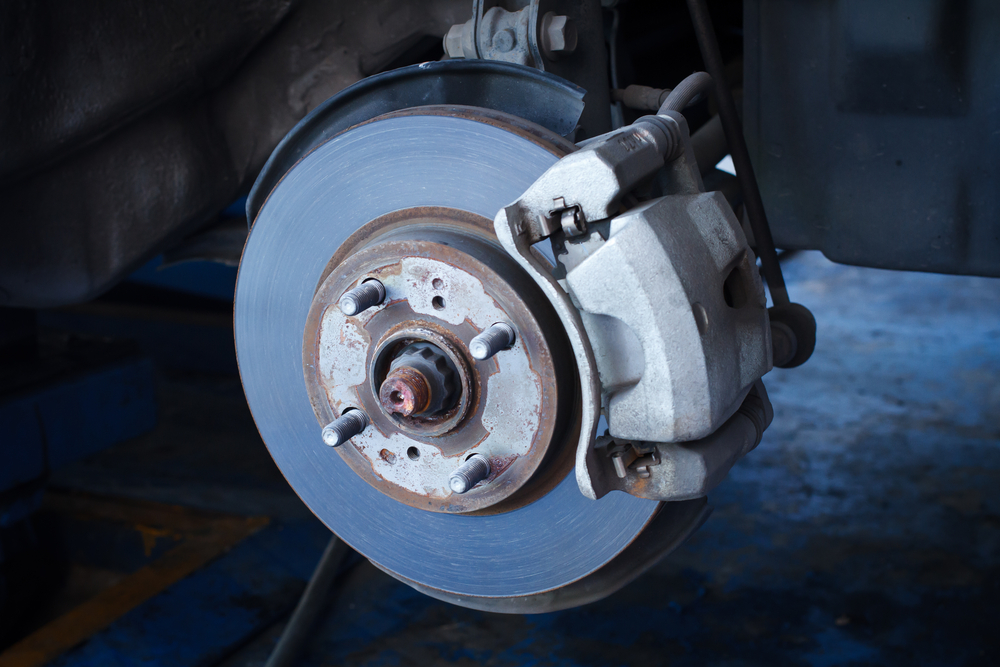
Annualized savings / site
Sales gain via capacity
Less RM, WIP & FG
Quality improved
Lean Leaders
Establish a global performance system to drive OpEx.
A leading automotive parts manufacturer selected Kaufman Global to support their efforts to improve profitability and competitiveness. The change was initiated during a time of significant business headwinds which included: a merger, the introduction of new products, union organizing efforts, and a drop in demand of 50 percent. In addition to the competitiveness improvements made during the project, considerable effort was applied to accelerate the sites’ adoption and practice of a “Continuous Improvement” culture. This was done through adoption of Kaufman’s SLIM-IT® approach to implementation and sustainability. In-house facilitators were given intensive hands-on training, enabling them to lead change efforts. LDMS was implemented within all workgroups to drive ownership at the shop floor level, and Executive Steering Committees were formed to give structure to the site leadership teams who were directing improvement efforts. Rapid Improvement Events drove impactful process changes. With the bespoke system generating the desired changes at a steady pace, the client went on to spread it’s Continuous Improvement performance system throughout all of its 120+ plants in over 25 countries.
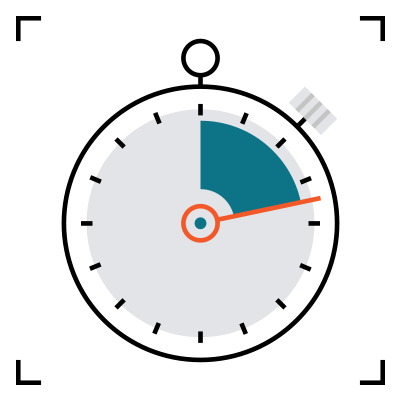
“… this has enabled us to sweep off the table what might have been 30 or 40 programs with various adoption rates and say, ‘Okay, that’s it. This is our program, our culture, our way of life.'”
Get Results
Like These.
Real organization change requires fast action, fast impact and enduring confidence in their results. Put Kaufman Global to work for you.