Project Highlights
Define a plan to support cost reduction, growth and Lean adoption
Seasonal business requires flexibility to intro counter-cycle products
Significant mfg. issues: scrap, rework, incorrect BOMs / drawings
New ERP system unable to perform properly given the above
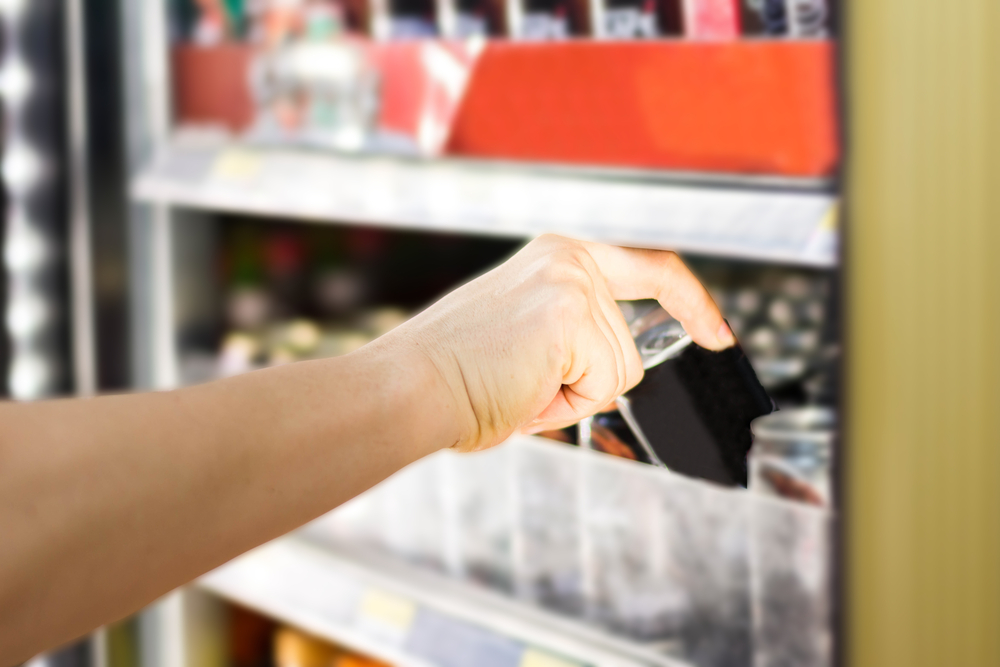
Less inventory
Reduction in floor space
Productivity increase
Faster order-to-ship time
Site members involved
Establishing a baseline to propel production excellence.
This client needed to rapidly reduce costs and propel growth within their commercial product lines. A three-week analysis revealed an organization fighting out-of-control business, manufacturing and IT processes that were resulting in production delays and angry customers. Kaufman Global developed a lean implementation plan that would aggressively address inventory, supply chain and productivity opportunities while enabling the desired production site capability.
The day after the analysis ended, the client requested we immediately begin implementation. Meaningful successes were achieved within the first week and included the decision of three valued-but-frustrated supervisory-level staff who had planned to resign deciding to stay.
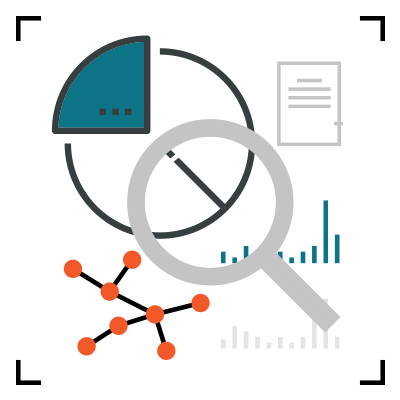
“This is how we are going to run and improve the business into the future. It’s not a step function; it’s a radically different expectation for everyone and that’s what’s required to make it work.”
VP, Manufacturing
Get Results
Like These.
Real organization change requires fast action, fast impact and enduring confidence in their results. Put Kaufman Global to work for you.