Project Highlights
Implement Lean across all office functions at NA HQ
Cost-savings, avoidance, cycle time, customer service
Lean, Office Kaizen and Six Sigma methods employed
Reach extended to include distribution and manufacturing
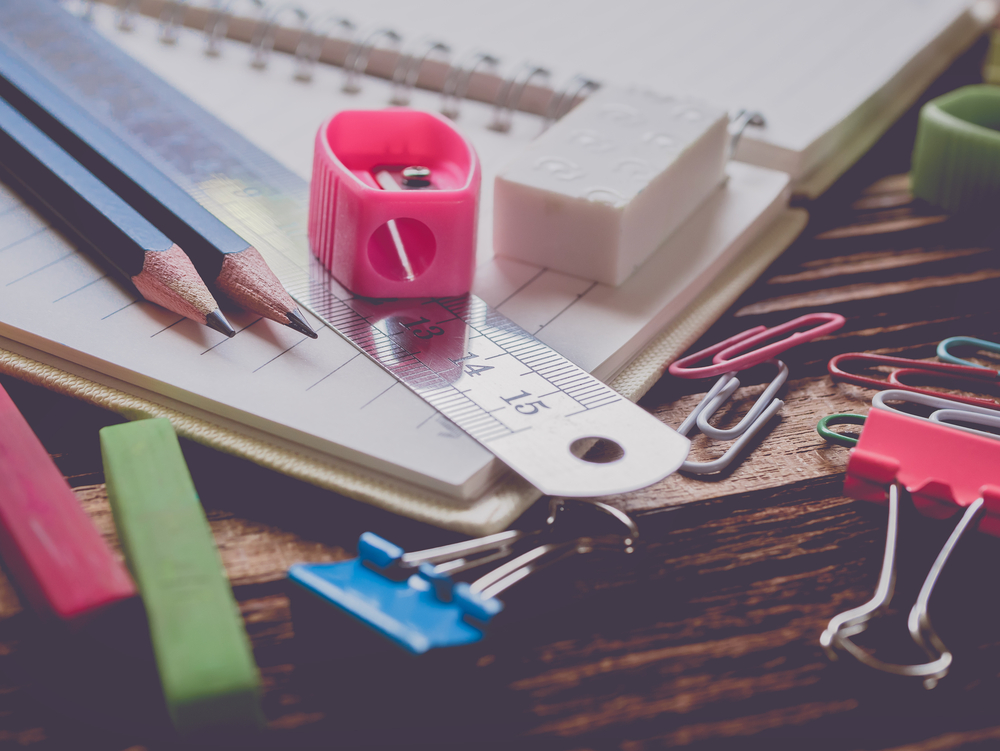
Annualized savings by YE
Faster to single # forecast
Faster call center response time
Employees engaged
Lost time incidents
Drive business results on the “Top Five” burning platforms.
A global manufacturer and marketer of consumer products wished to implement Lean across all office functions within their North American headquarters and to integrate those activities with similar Lean implementations at its manufacturing sites. Partnering with Kaufman Global the Leadership Team determined the “Top Five” priority areas for in-depth Lean assessments and implementation over a focused 100-day period. Work teams were established to address the selected functions which included product development, supply chain quality, data integrity, seasonal peak processing, and demand management.
Lean tools and techniques, including Rapid Improvement Events, Lean Daily Management System® (LDMS®) methodology and the 20 Keys® methodology were merged with the client’s existing Six Sigma methodology to provide a holistic approach to implementing change across the organization.
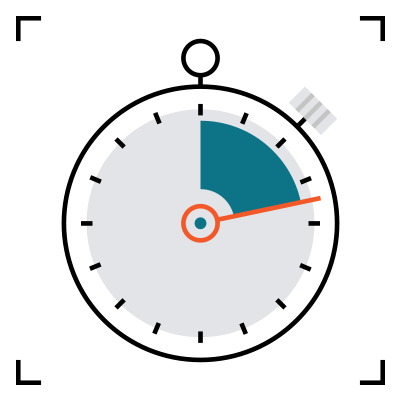
“I came into this event with very high expectations. I saw it as a last ditch effort to fix a problem that we have been trying to resolve for the past two and a half years. I’m ecstatic at what you have all done in just three days. We have to do this kind of thing all through the supply chain.”
Get Results
Like These.
Real organization change requires fast action, fast impact and enduring confidence in their results. Put Kaufman Global to work for you.